Products
All-In-One Workstations
Combining all of our solutions into one headline product. SmartRack is ready to service your full-automation needs from Product Tracking, Workorder Checklists, Employee Access, up to 14 Environmental Sensors, Label Printing, and a custom web-enabled User Interface
Equipment Control
Easily connect, control, and automate your equipment using communication protocols such as SECS/GEM, Serial, MODBUS, and more. Create macros for driving tool-setup and starts, and event handlers to respond to alarms or signals.
Product Tracking
Utilize Wireless or Barcode inventory stations to track products throughout the factory. Monitor the usage and lifetimes of chemicals and consumables. These standards are well known for use with contactless communication and tracking of RFID Labels, Pills, ID Cards, Wristbands, and more.
Label Printing
Connect to a variety of printers such as Zebra, EPSON, SATO to print tracking labels for your products such as Barcodes, QR Code, or Plain Text. Integrate with RFID printers and print labels that track throughout the facility.
Sensors
I/O Modules and 5v sensors can be connected with our product to gain insights on your workspace and automate common tasks. Monitor your environment using proximity sensors, motion detectors, light, temperature, pressure sensors, buttons, and more.
HMI/SCADA
Human Machine Interfaces are tools which allow operators to manage the Control and Data Acquisition of industrial equipment. CAB provides custom HMI's built in a familiar web-enabled interface allowing the ease of adoption and a superior user experience.
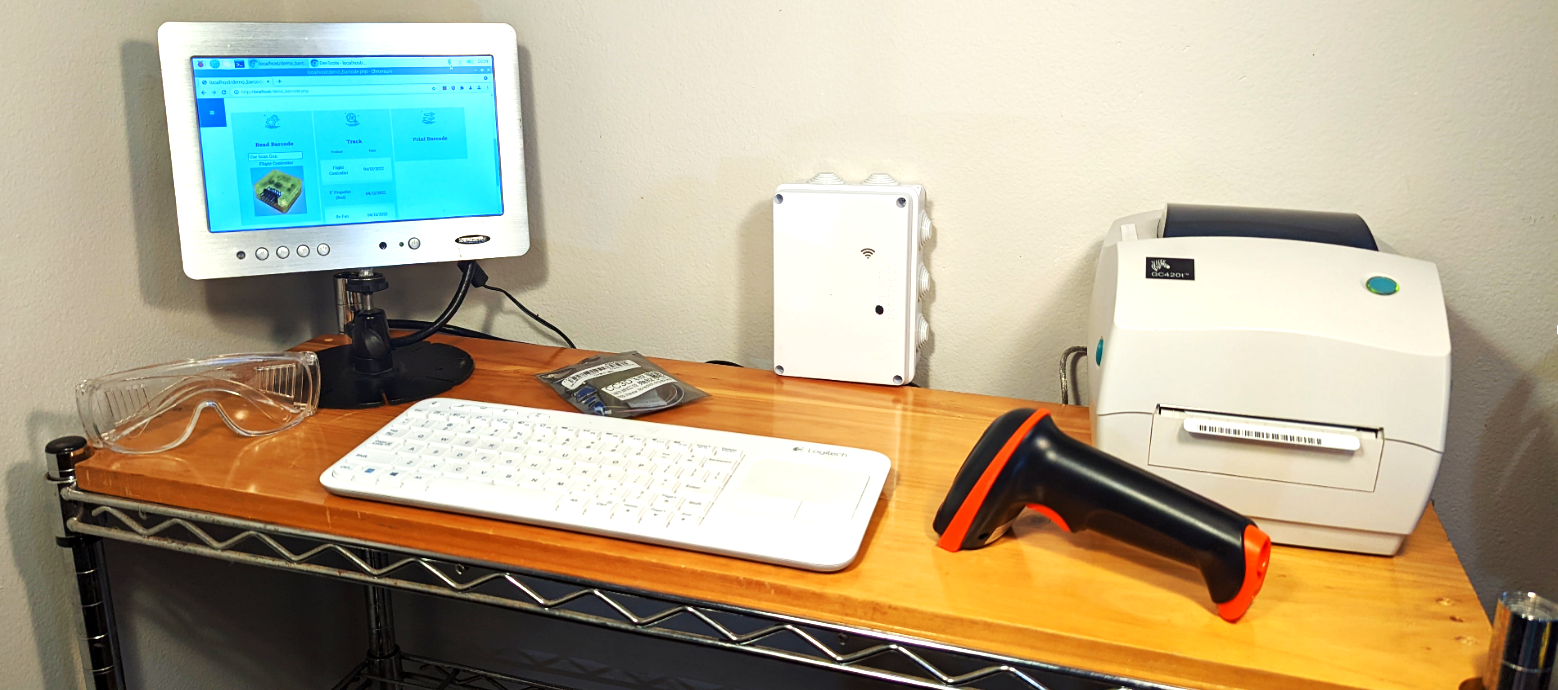
Services
Engineering
All projects begin at the requirements-gathering phase. During this step we will review your existing automation solutions, and deep dive into the current project needs. A scope of work document will highlight the expectations of the project and confirm the software and hardware requirements. Once approved, projects are resolved and rigorously bench tested.
Installation
Installation is a critical component of the project delivery, as floor-space is highly valuable. Once a solution has been created, it is delivered onsite to be integrated onto the shop floor; the location should be equipped with at minimum a 120v A/C outlet and optional network connection. This step allows the operator to interface with the solution and ensure the correct sequence of operations.
Commitment
Our solutions are commissioned for you, and supported by us. Parts are replaced on demand, and issues or upgrade requests are handled through our ticketing service. Solutions are leased or rented and installation is handled by our experts. Once deployed, our solutions come with a guarantee of operability.
Schedule a Demo
In-person appointments can be made to demo the functionality of our products directly on your production floor. With several built-in features, our workstations are likely to start producing results immediately. Submit a request online and a solution expert will contact you shortly.